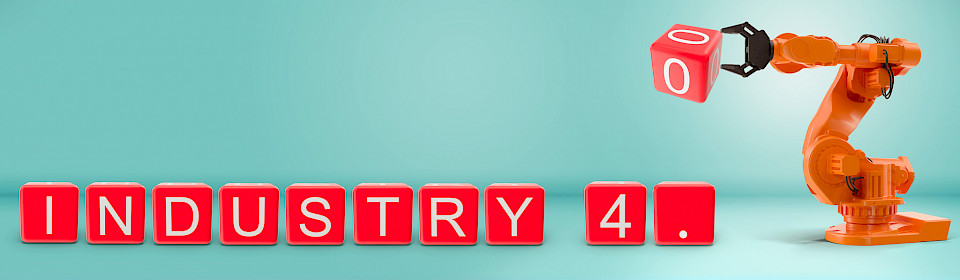
Wie kann der Digitale Zwilling das produzierende Gewerbe in die Zukunft befördern?
Industrie 4.0 steht für die umfassende Digitalisierung der industriellen Produktion und bringt zahlreiche Konzepte und Technologien mit sich. Eines der faszinierendsten Teilkonzepte dabei ist der digitale Zwilling.
Diese virtuelle Abbildung ermöglicht uns, Prozesse zu simulieren, optimieren und zu überwachen. In meiner beruflichen Laufbahn gehörte die Arbeit mit physischen Maschinen jahrelang zu meinem Alltag. Umso faszinierender war damals die Vorstellung, eine digitale Repräsentation dieser Maschinen zu nutzen.
Der digitale Zwilling ist nicht nur ein technisches Konzept, sondern ein Symbol für die tiefgreifende Transformation in unserer Industrie. Er ermöglicht es, Produktionen effizienter zu gestalten oder Wartungen zu optimieren. Die Chance, an der Spitze dieser technologischen Revolution zu stehen, hat mich dazu motiviert, mich selbst neuen Herausforderungen zu stellen.
Ein entscheidender Moment für meine Begeisterung für den digitalen Zwilling war mein Besuch auf der Messe World of Tools von der Firma Hoffman Group in Nürnberg. Hier hatte ich zum ersten Mal die Gelegenheit, eine Live-Vorstellung dieser Technologie zu sehen.
Die Demonstration zeigte, wie digitale Zwillinge in Echtzeit arbeiten und welche Einsatzmöglichkeiten diese haben. Die Präzision und die diversen Einsatzbereiche haben mich direkt begeistert. Dieses Erlebnis bestärkt mich dabei, tiefer in die Digitalisierung der Industrie einzutauchen.
Mein Fokus ist dabei das Konzept des digitalen Zwillings und der Zusammenhang zu Industrie 4.0. Im folgenden Artikel gehe ich diesen Fragen nach:
Was versteht man unter einem digitalen Zwilling?
Industrie 4.0 ist die Bezeichnung für Projekte zur umfassenden Digitalisierung der industriellen Produktion. Ein Konzept daraus ist der digitale Zwilling.
Der digitale Zwilling ist die digitale Repräsentation eines materiellen Objekts.
Dabei ist es nicht ausschlaggebend, ob das physische Objekt bereits existiert oder erst existieren wird. Die Grundidee bleibt jedoch, dass alle Daten über eine einheitliche Schnittstelle abgerufen werden können.
Warum ist ein digitaler Zwilling so wichtig für die Industrie 4.0?
Kurz und pragmatisch zusammengefasst:
Ein digitaler Zwilling kann alles sein – von einem realen, schon existierenden Werkzeug bis hin zu einem noch entstehenden Werkstück.
Weiterhin kann es sich dabei auch um eine ganze Produktionslinie handeln, die sich noch im Aufbau befindet. Allerdings stehen die Daten zur geplanten Auslastung jetzt schon zur Verfügung.
Wie profitieren Unternehmen davon?
Wie kann also mein Unternehmen von der bereits laufenden Digitalisierung und speziell dem Digital Twin profitieren? Dazu sollten wir uns zuerst die geplante und ungeplante Stillstandszeit ansehen.
Der geplante Stillstand entsteht, wenn in der Produktion nicht genügend Auslastung vorherrscht. Diese kann durch mangelhafte Planung, ungenaue Vorhersagen oder langsame Bürokratie im Fertigungsprozess entstehen. Ein ungeplanter Stillstand passiert, wenn Wartungen in der Produktionskette anstehen oder Störungen die Produktionskette lahmlegen.
Beiden Stillstandszeiten können Unternehmen mithilfe eines digitalen Zwillings entgegenwirken. Die Vision der vollkommenen Auslastung aller Maschinen wird mit einem Digital Twin umgesetzt:
-
Optimierung der Produktionsplanung: Durch die Simulation verschiedener Produktionsszenarien können Unternehmen die bestmöglichen Produktionspläne erstellen. Der digitale Zwilling analysiert historische Daten und prognostiziert zukünftige Bedarfe, sodass Maschinen besser ausgelastet werden.
-
Nachfrageänderungen in Echtzeit: Mit einem digitalen Zwilling können Unternehmen schnell auf Veränderungen in der Nachfrage reagieren. Echtzeitdaten ermöglichen es, Produktionspläne dynamisch anzupassen, um Auslastungsschwankungen zu minimieren.
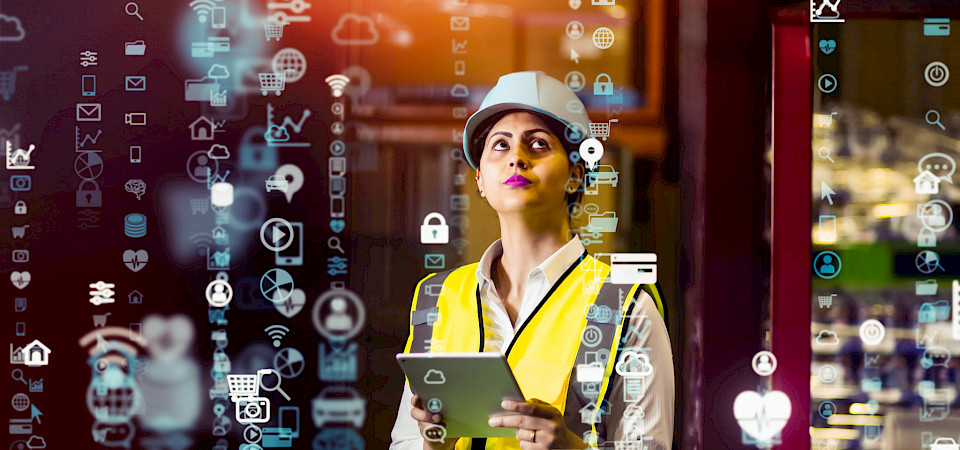
Ungeplante Stillstandszeiten können die Produktivität erheblich beeinträchtigen. Sehen wir uns auch hier die Möglichkeiten an:
-
Predictive Maintenance: Mit einer kontinuierlichen Überwachung des Maschinenzustands in Echtzeit oder durch die Analyse von Sensordaten kann der digitale Zwilling potenzielle Probleme frühzeitig erkennen. So lassen sich vorausschauend Wartungsarbeiten planen, bevor es zu Ausfällen kommt.
-
Fehlersimulation: Unternehmen können auch verschiedene Störungsszenarien simulieren und analysieren. Dies hilft dabei, schnellere und effektivere Lösungen im Falle einer Störung zu finden.
Abgesehen von dem unproduktiven Stillstand, hat eine virtuelle Abbildung noch so viel mehr Potenzial. Die bereits erwähnte zentrale Schnittstelle spielt dabei eine tragende Rolle:
Alle Daten der unterschiedlichsten Fertigungsschritte in einem Unternehmen werden zentral zusammengetragen – von der Werkzeugausgabe in der maschinellen Fertigung bis hin zur Warenannahme des gelieferten Halbzeugs.
Was daraus resultiert, ist eine Reduzierung aller Fertigungskosten.
Fachkräfte müssen nicht auf das Go aus der Abteilung des vorherigen Fertigungsschrittes warten. Sie können mit der Arbeit des nächsten Fertigungsschritts schon vorzeitig beginnen. Das möchte ich an einem Beispiel verdeutlichen:
Die Fachkraft in der Werkzeugausgabe kann mit ihrer Arbeit schon beginnen, bevor der Auftrag hierarchisch durchgereicht wird.
Ist der Produktionsauftrag im System und der digitale Zwilling gibt das Startzeichen, kann bereits mit dem Rüsten begonnen werden. Auch wenn das Rohmaterial noch auf dem Lieferweg ist.
Das hat wiederum Auswirkungen auf die internen Prozesse. Die Produktionsqualität steigt, da die Daten gespeichert und ins System zurückgeführt werden.
Vor dem nächsten Produktionszyklus können diese Daten analysiert werden. So lassen sich Fehler erkennen und Prozesse können (etwa durch „Big Data“ Methoden) optimiert werden.
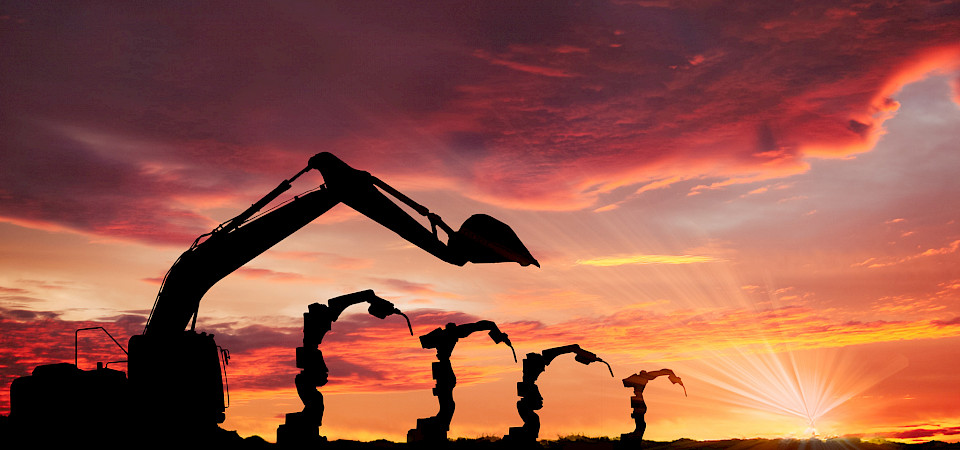
Welche Herausforderungen haben Unternehmen?
Ein so komplexes System lässt sich nicht so einfach umsetzen. Voraussetzung sind präzise und verlässliche Daten. Die Integrität dieser Daten ist entscheidend.
Ungenaue Daten könnten zu falschen Entscheidungen führen.
Oder einfach gesagt: “Ein solches System funktioniert nur, wenn man es richtig pflegt!”
Weiterhin muss ein digitaler Zwilling mit verschiedenen Systemen und Technologien interoperieren, damit dieser nahtlos funktionieren kann. Dies beinhaltet:
-
die Integration von Software,
-
Hardware und
-
Netzwerklösungen verschiedener Anbieter.
Prozesse, Systeme und Menschen müssen ineinandergreifen.
Ebenso sollte die Datensicherheit gewährleistet sein. Da digitale Zwillinge auf einer Vielzahl von Datenquellen basieren, ist der Schutz dieser Daten von größter Bedeutung. Cyberangriffe und Datenschutzverletzungen könnten schwerwiegende Folgen haben.
Nicht zu vernachlässigen sind organisatorische Herausforderungen: Die Einführung neuer Technologien kann auf Widerstand innerhalb des Unternehmens stoßen. Mitarbeitende müssen geschult und überzeugt werden, die neuen Systeme zu akzeptieren und effektiv zu nutzen.
Die Implementierung eines Digital Twins erfordert erhebliche finanzielle Investitionen in Technologien, Infrastruktur und Fachwissen. Aber hier sollten Sie nicht den Weg aus den Augen verlieren! Sie investieren in Ihre Zukunft und in einen Prozess, der sich erst mit der Zeit entfalten lässt!
Diese Unternehmen können Digital Twin - inspirierende Beispiele
Siemens
Die Produktionslinie in Nanjing, China, ist das Vorzeigeprojekt von Siemens, bei dem der digitale Zwilling zum Einsatz kommt. Während der Pandemie wurden dort drei Produktionsstandorte zu einer schlanken, umweltfreundlichen Digital Native Factory zusammengeführt.
Im Vergleich zu den ursprünglichen Anlagen stieg
-
die Produktivität um 20 %,
-
die Flexibilität um 30 %
-
und die Geschwindigkeit des Materialnachschubs um 50 %.
Der entscheidende Faktor für diesen Erfolg? Die Umsetzung des Werks zunächst als digitaler Zwilling, bevor die physische Zusammenführung der Fabriken erfolgte. Siemens investierte erst kürzlich zum erneuten Mal in diese Technologie. Damit unterstreicht der deutsche Konzern die Bedeutung des digital Twins für die Industrie.
BMW
Auch in Deutschland kommt die digitale Zwillingstechnologie bereits zum Einsatz – beispielsweise bei BMW.
In der iFACTORY wird die Digitalisierung auf ein neues Level gehoben. Hier wird eine durchgängige Datentransparenz über die gesamte Wertschöpfungskette und alle Prozesse hinweg implementiert. Dies ermöglicht eine hocheffiziente digitale Prozessgestaltung.
BMW plant, eine digitale Abbildung aller Produktionslinien zu erstellen – inklusive Maschinen und Mitarbeitenden. Dadurch können neue Fahrzeugmodelle nahtlos in bestehende Produktionslinien integriert und umfangreiche Analysen durchgeführt werden.
Somit liefert der digitale Zwilling nicht nur Informationen zur Produktionsmenge, sondern auch spezifische Daten zu den Fahrzeugmodellen. Diese helfen, die Konstruktion gezielt zu unterstützen.
Statt der herkömmlichen, hierarchischen „Wasserfall“-Struktur, bei der Informationen von oben nach unten – von der Konstruktionsabteilung bis zum Fließband – weitergegeben werden, ermöglicht der digitale Zwilling eine flexible, vernetzte Kommunikation in alle Richtungen.
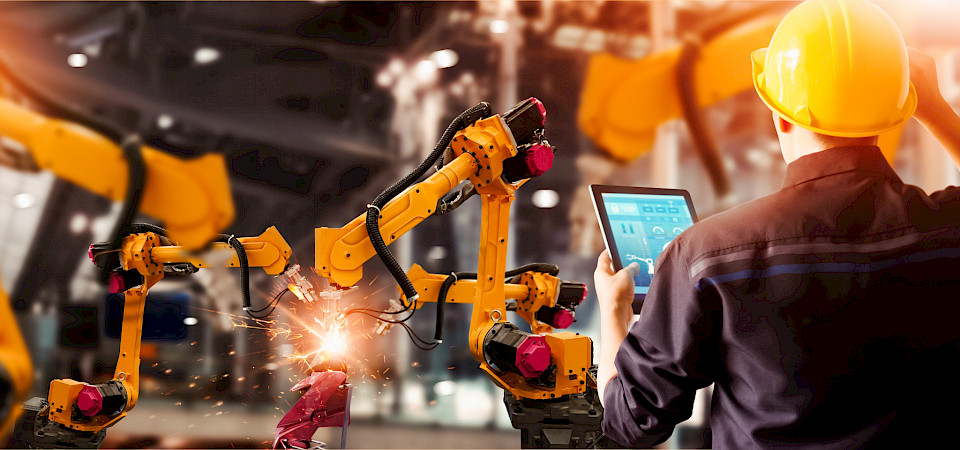
Fazit und Zukunftsausblick
Mein beruflicher Wechsel aus dem produzierenden Gewerbe in die Softwareentwicklung hat mir meine Meinung bestätigt. Die Verbindung von traditioneller Industrie und moderner IT ist faszinierend und voller Potenzial.
Jeden Tag arbeite ich daran, Brücken zwischen diesen Welten zu schlagen und die Industrie 4.0 voranzutreiben.
Mein Weg beweist, dass es nie zu spät ist, etwas Neues zu beginnen und sich den Herausforderungen der Zeit zu stellen. Die Digitalisierung ist nicht das Ende der traditionellen Berufe, sondern ihre Evolution. Und ich bin stolz, Teil dieser Entwicklung zu sein.
Dieser Beitrag soll anderen Mut machen, den Schritt in eine neue Richtung zu wagen. Die Zukunft ist digital, und sie bietet unzählige Möglichkeiten für diejenigen, die bereit sind, sich anzupassen und weiterzubilden. Sein Sie offen für Veränderungen! Mit jambit können Sie Ihre Reise in die Industrie 4.0, selbst gestalten!